AMbition
- Infrastructures
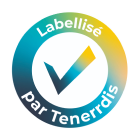
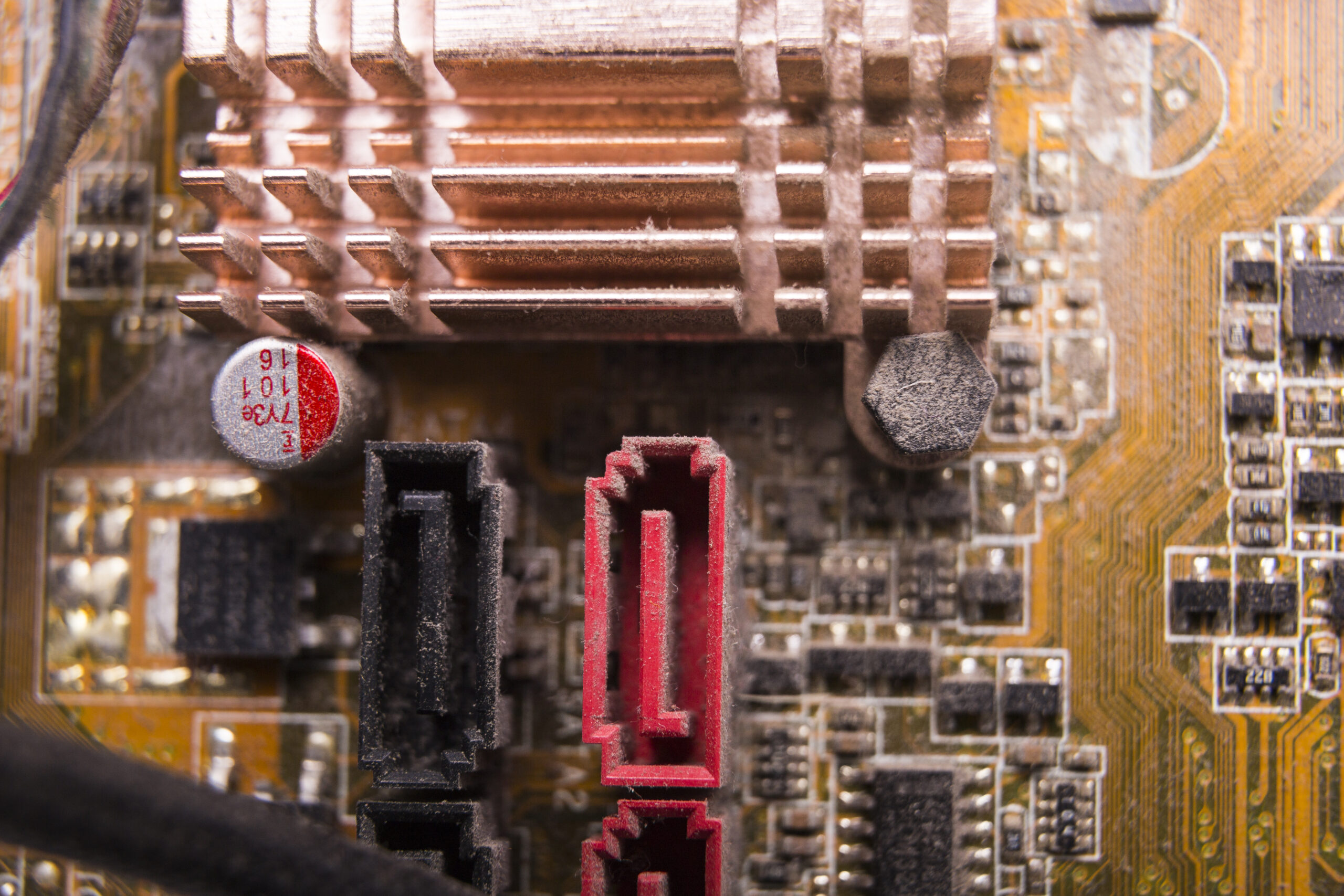
Améliorer des moyens de fabrication additive métallique, et plus spécifiquement le développement du procédé pour les matériaux à base de cuivre.
Améliorer l’efficacité énergétique de la production de certains matériaux
L’enjeu principal de ce projet est d’évaluer et mettre au point des stratégies afin d’appliquer le cuivre (par fabrication additive), essentiellement pour 2 types de matériaux : des pièces conductrices électriques pour Schneider Electric et Stellantis, et des pièces esthétiques pour Stellantis et Varinor. Cette application permettant ainsi d’améliorer l’efficacité technique et énergétique des différentes pièces lors de leur utilisation.
Comment ça marche concrètement ?
Le cuivre pur réfléchit l’essentiel du rayonnement infrarouge lorsqu’il est à l’état solide. De ce fait, les lasers de 400W, utilisés généralement sur les machines de fusion laser sur lit de poudre, ne permettent pas d’obtenir des microstructures suffisamment denses pour générer des propriétés intéressantes pour les applications électriques. Il existe plusieurs stratégies de contournement de cette problématique :
- Utiliser des éléments d’alliages. Cette solution induit une chute de la conductivité électrique mais peut constituer un compromis intéressant pour les applications esthétiques.
- Utiliser un laser infrarouge plus énergétique (>800W).
- Utiliser un laser ayant une longueur d’onde différente, permettant de limiter la réflectivité du matériau : laser vert, laser bleu
- Appliquer un revêtement sur les poudres, de manière à limiter la réflectivité du matériau sous un laser infrarouge
- Utiliser le procédé de fusion sur lit de poudre par faisceau d’électrons
11 partenaires complémentaires pour apporter des solutions
Les différents partenaires ont apporté leur expertise et leurs compétences pour explorer l’ensemble de ces 5 solutions, depuis l’élaboration des poudres et leur transformation, jusqu’à leur mise en œuvre dans les machines de fabrication additive, la modélisation des procédés et la compréhension de la physique de l’interaction faisceau-matière, pour terminer par des reconceptions de composants pour la fabrication additive et les essais fonctionnels produits.
Partenaires industriels :
- Schneider Electric, spécialiste des équipements et services pour la gestion de l’énergie et les automatismes industriels / chef de file du projet
- AddUp, fabricant de machines de fabrication additive, filiale commune de Michelin et de Fives
- Stellantis, constructeur automobile
- Varinor, groupe Richemont, joaillerie et luxe
- Lifco Industrie, groupe HEF, spécialiste de la fonctionnalisation de poudres
- ESI Group, spécialiste du développement de logiciels pour la modélisation des procédés
Partenaires académiques (laboratoires), regroupés autour du CNRS :
- LPGP (Orsay)
- SIMaP (Grenoble)
- G-Scop (Grenoble)
- PIMM (Paris)
- LERMPS (Belfort)
Les recettes permettant la mise en œuvre du cuivre et de certains de ses alliages par ces technologies ont été mises au point pour satisfaire aux cahiers des charges des différents cas d’application. En ce qui concerne la conductivité électrique par exemple, le procédé E-PBF mis au point par le SIMaP permet d’atteindre 100% IACS ; le procédé L-PBF mis au point par AddUp permet d’atteindre 98% IACS.
Un projet labellisé Tenerrdis
Ce projet innovant labellisé par Tenerrdis a été sélectionné dans le cadre du 24e appel à projets du FUI-Régions. Il s’inscrit parfaitement dans la feuille de route de Tenerrdis qui place la maîtrise des consommations énergétiques et la digitalisation de l’énergie au cœur de sa stratégie. Depuis 2005, l’ensemble des appels à projets du FUI a permis de soutenir 61 projets labellisés par Tenerrdis, pour un budget total de 220 M€ et un financement public de 83 M€.
Le projet AMbition a été financé avec le concours de la région Auvergne-Rhône-Alpes, la région Ile-de-France et la BPI.
En savoir plus
Dates
Un budget de
5,6M€Un projet porté par
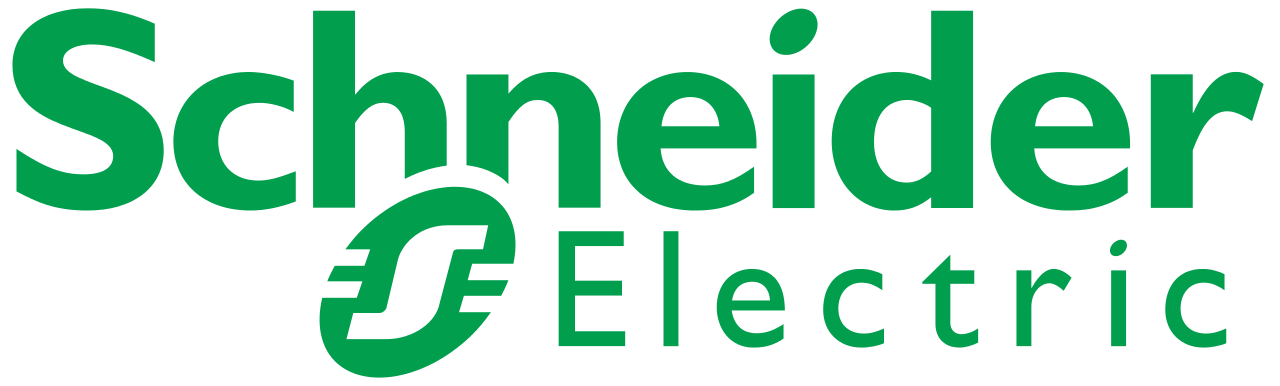
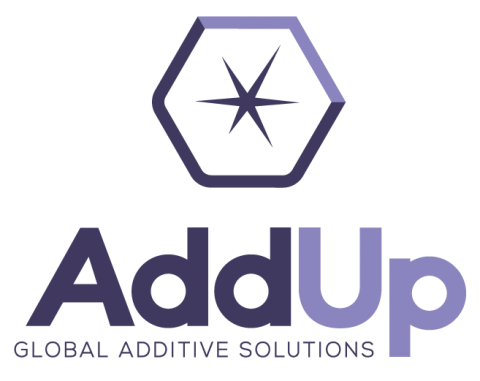
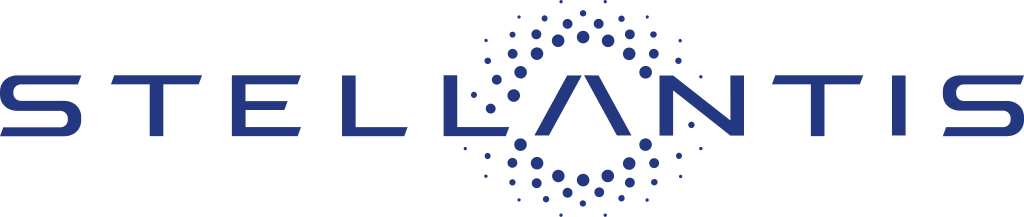
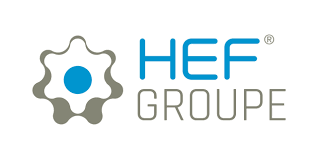
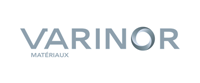
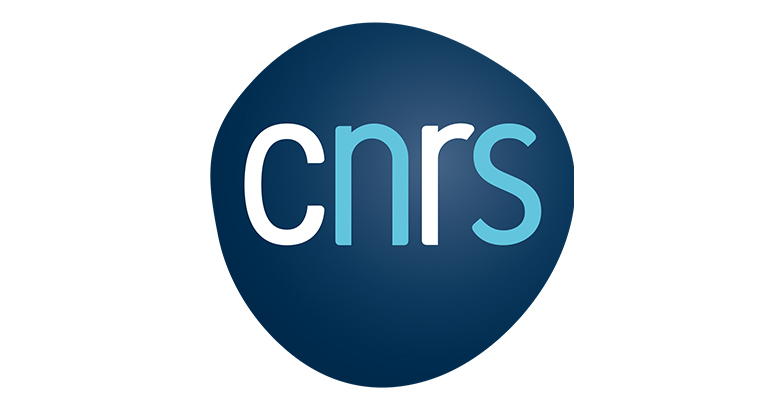
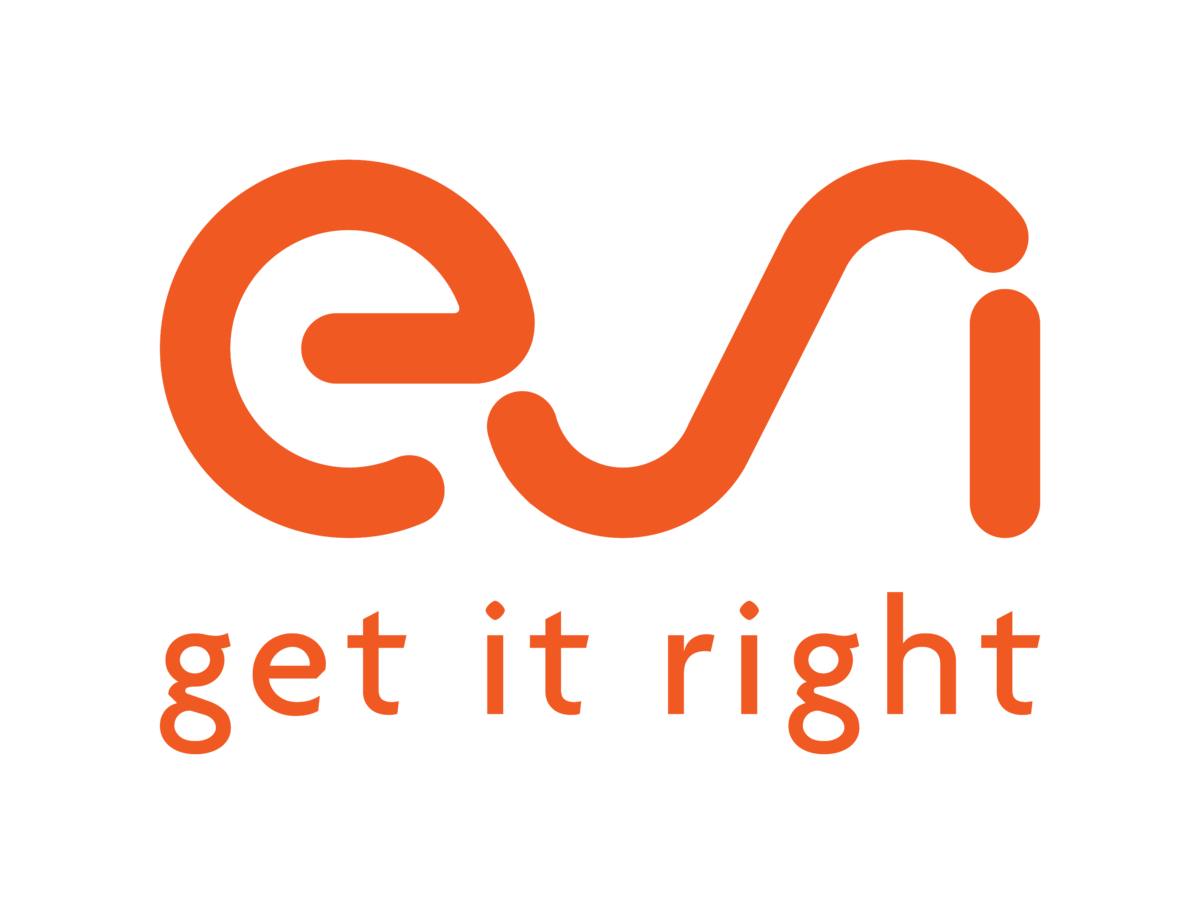
Financeurs
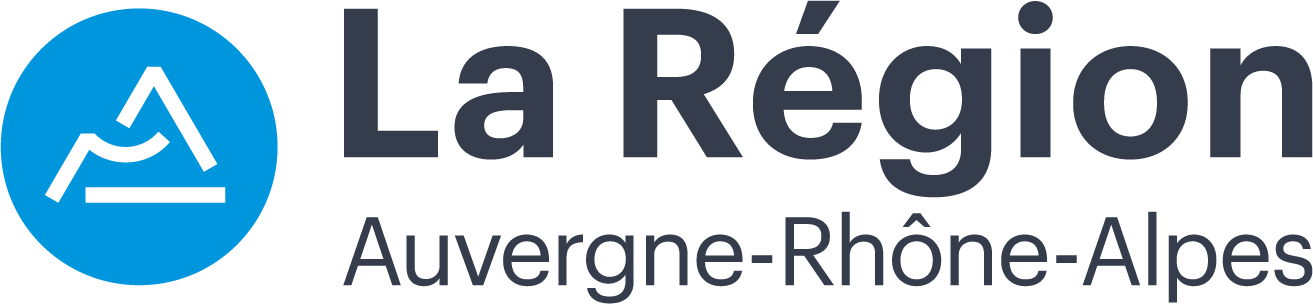
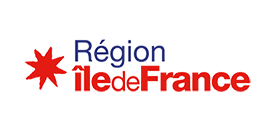
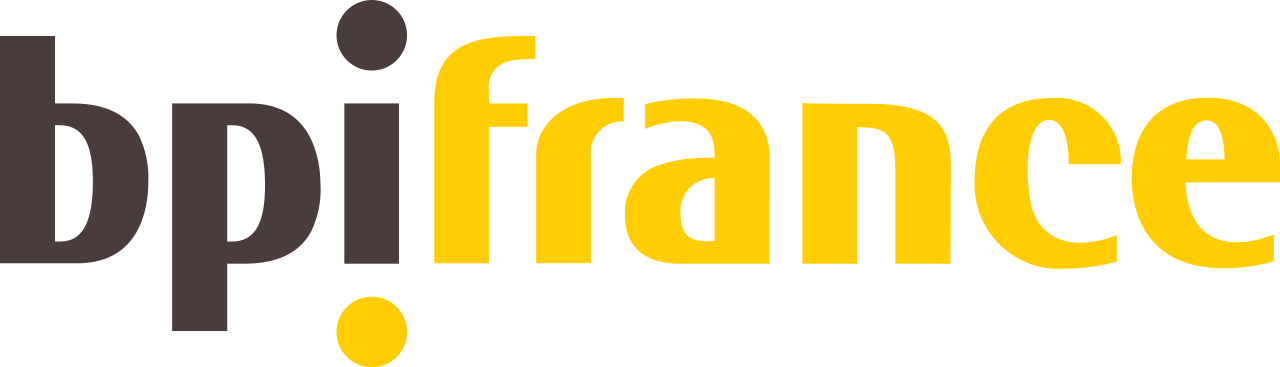
Rôle de Tenerrdis
Tenerrdis a accompagné et labellisé ce projet.
Témoignage
Guillaume Fribourg,
Materials industrialization engineer,
Schneider Electric
A l’issue du projet, je peux dire que la performance technique est au rendez-vous et que nous sommes maintenant capables de mettre en œuvre le Cuivre par la fabrication additive, avec des propriétés compatibles avec nos besoins industriels. Il reste en revanche encore du chemin à parcourir pour déployer la fabrication additive à l’échelle industrielle, de manière à bénéficier pleinement du potentiel de ces technologies clefs pour notre compétitivité future.